Implementation
Increase enterprise profits by building efficient business processes in a single system
- 20+ years of practice (projects include Siemens, BIOCAD, Hygiene Kinetics, Tablogix, Shell, Teboi)
- Proprietary project technology - tested on 200+ cases
- 300+ certified specialists - we will assemble a relevant team for your project.
- Maximize the use of standard functionality - reduce the cost of future enhancements
1C ERP: The Fully Functional Alternative to SAP in Russia
SAP company suspended operations in Russia. 1C: ERP system is now the only alternative local solution. assino experts can also integrate 1C with SAP or make a transition from SAP to local 1C solution to ensure compliance with legal requirements in Russian Federation.
What tasks 1C:ERP implementation solves

Full control over business management in a single system
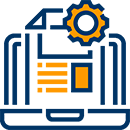
Automation of all processes in the company
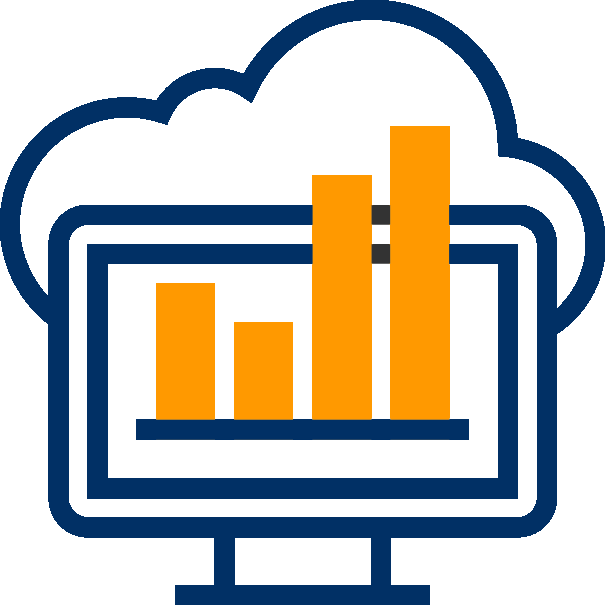
Replacing a large number of programs with a single solution
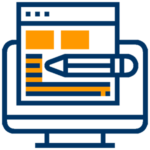
Migration from self-written and customized software to reduce costs
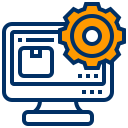
Import substitution of vendors that left the Russian market (SAP, Oracle, MS Dynamics, etc.)
For whom the solution is useful
Main Functions
Production automation
Opportunities:
- Flexible production planning.
- Control over compliance with production plans.
- Informing about the process of production preparation.
- Management of activities of inter-shop divisions.
- Intra-shop production management.
- Optimization of production time and product cost.
- Visualization of production planning results.
- Reduction of labor costs for intra-shop document management.
- Control of receipt of necessary resources for production.
- Calculation and rationing of production costs.
Monitoring and analysis of production indicators
Key features:
- building a model of indicators with visualization;
- monitoring and comparison of target indicators;
- analysis of financial indicators by activity areas;
- a wide choice of visualization forms for displaying reports;
- the ability to monitor indicators from any device and customize the sending of reports to mail.
Equipment repair and maintenance
Functions:
- collection and storage of information about operated objects and their parameters;
- planning of maintenance of objects;
- registration of equipment output;
- planning of repairs.
Financial management
Features:
- cost accounting for each line of business;
- accounting and detailing of the cost of production;
- planned calculation of output;
- reporting of financial results;
- prevention of cash gaps;
- detailed financial analysis;
- tools for creating budget forms;
- performance analytics on planned outputs;
- performance analytics by planned indicators;
- automation of the budget process;
- visualization of information for budget planning control.
IFRS accounting and reporting
Features:
- setting up a chart of accounts for financial accounting;
- using rules and templates to display entries in the accounting;
- preparation of financial statements using the report generator.
Inventory and warehouse management
Features:
- management of layout, assembly, movement of goods thanks to addressable storage;
- automatic selection of a place for storing goods;
- creation of working zones for optimal access to storage cells, formation of the order of bypassing storage cells;
- optimization of goods placement with the help of order picking strategies;
- maintenance of goods accounting;
- optimization of logistics and delivery processes.
Procurement management
Capabilities:
- determination of warehouse and production needs;
- procurement planning;
- display of the whole purchasing cycle in the system;
- maintaining the history of purchases, accounting of suppliers by the degree of their reliability;
- accounting of procurement documentation;
- automatic registration of supplier prices;
- management of statuses and states of orders to the supplier;
- support of various schemes of internal document flow of procurement activities.
Sales and pricing management
Features:
- wholesale sales management;
- retail sales automation;
- mobile application for the work of sales representatives;
- flexible pricing: maintenance of several types of prices in different currencies, use of standard and individual price agreements;
- reporting to control commission trading;
- tools for delivery management;
- analytical reports.
Cost management
Possibilities:
- planned calculation of output;
- convenient wizard for closing the month;
- customized reporting for displaying the financial result.
Business result from implementation
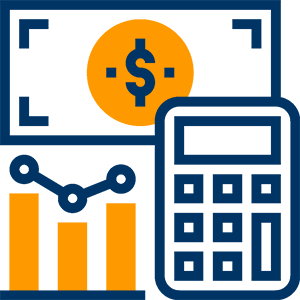
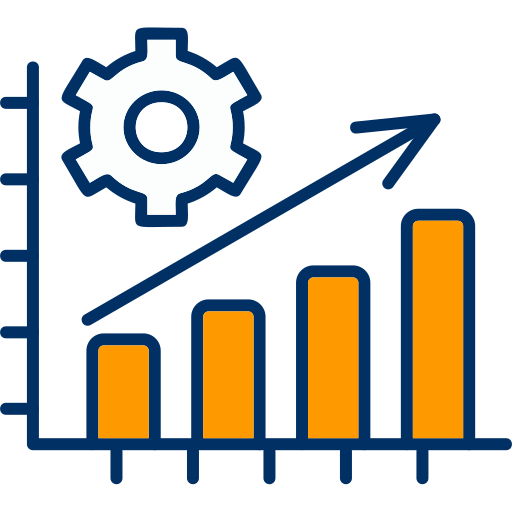
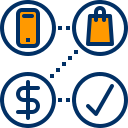
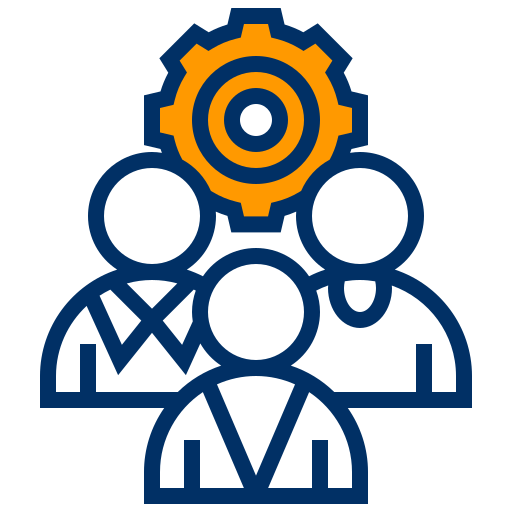
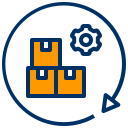
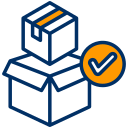
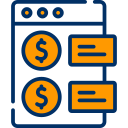

At the expense of which results are achieved:
- Building an end-to-end MRP chain in the system allows the purchasing department to track the planned dates of material requirements for production. Taking into account the delivery time, the purchasing manager knows exactly when the material needs to be ordered. In this way it is possible to avoid buying material “in advance”, as well as to eliminate “stale” goods and freezing of money in materials in warehouses.
- Create a strategy to manage the end-to-end production process using MRP II methodology that takes into account not only operational but also financial planning. This allows you to establish a link between production and product demand, keep production running smoothly to meet the order schedule, and monitor results and adjust the schedule when changes occur.
- Due to the functionality of the system it is possible to increase the accuracy of planning and the quality of analysis of production processes, which allows you to identify “bottle necks” and eliminate inefficient production and downtime.
- Reflection of all business process operations in a single information system allows management accounting, regulated accounting, as well as accounting according to international standards to be kept in a single database. Due to the fact that any data can be tracked at the point of its origin, the reliability and timeliness of reporting increases.
Stages of implementation
- Audit of your business processes.
- Determination of the functionality required by the system.
- Selection of a relevant solution.
- Modeling of target business processes.
- Working out the scheme of integration with the existing IT landscape and with GIS.
- Definition of the residuals transfer concept.
- Presentation of a typical system model.
- Formation of the list of necessary improvements.
- Improvement of the system functionality by priority blocks within the budget defined at the modeling stage.
- Demonstration of improvements to users in video format.
- Preparation of tools for transferring balances.
- Test transfer of NSI and balances from the current system to the new one.
- Fixing the result criteria for tool management.
- Deployment of the information base.
- Transfer of NSI and balances of the operational contour.
- Preparation of instructions for data input into the system.
- Training of users to work with the 1C system.
- Support of the system launch into commercial operation.
- Consultation of users.
- Helping users to correct data.
- Processing of requests for development of the system functionality.
Benefits of implementation with assino
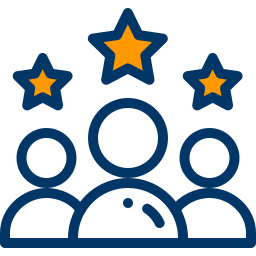
Proven experience
The project is supervised by a team of experienced experts who have implemented a number of automation projects both in large holdings and small companies.
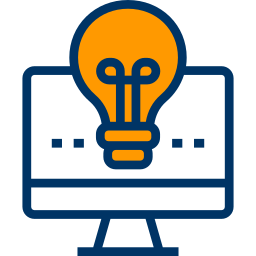
Ready-made solutions
We solve non-standard tasks within the framework of implementations, we have our own experience in this area, each new project is a concentration of expert experience of previous projects.
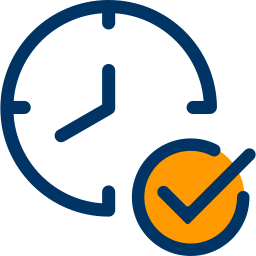
100% of the plan on time
We build transparent and trusting relationships with our clients: we do not exceed the budget, report on every stage of the project and always deliver projects on time.
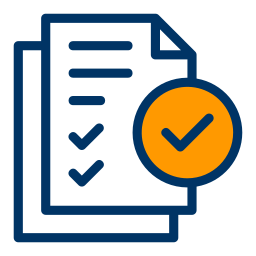
Quality documentation
Each stage of the project is closed with a document detailing the work performed. This simplifies further support and development of the system.

IT infrastructure
We will host your system on high-performance assino servers configured specifically for 1C:ERP and perform full optimization of 1C performance.
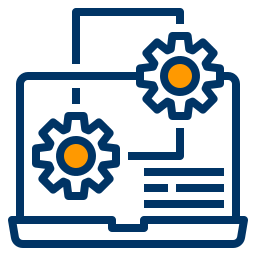
Technical support
Dedicated technical experts maintain stable system operation and quickly resolve problems within the framework of the service level agreement (SLA).
We
International consulting company –
the market leader in automation of international companies in Russia and the CIS countries. Professionals with proven experience and an implemented quality management system ISO 9001:2015
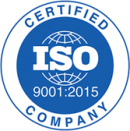
years of development and implementation of software solutions for ERP systems based on 1C products and their integration with SAP, Microsoft, etc.
completed projects
experts in business solutions practice with extensive technical experience
Do you have any questions about the digitalization of business processes?
Ask our experts.
Completing your tasks can be a lot easier!